Table of Contents
Related Articles
Building a Safer Landscaping Program For Schools & Cultural Institutions
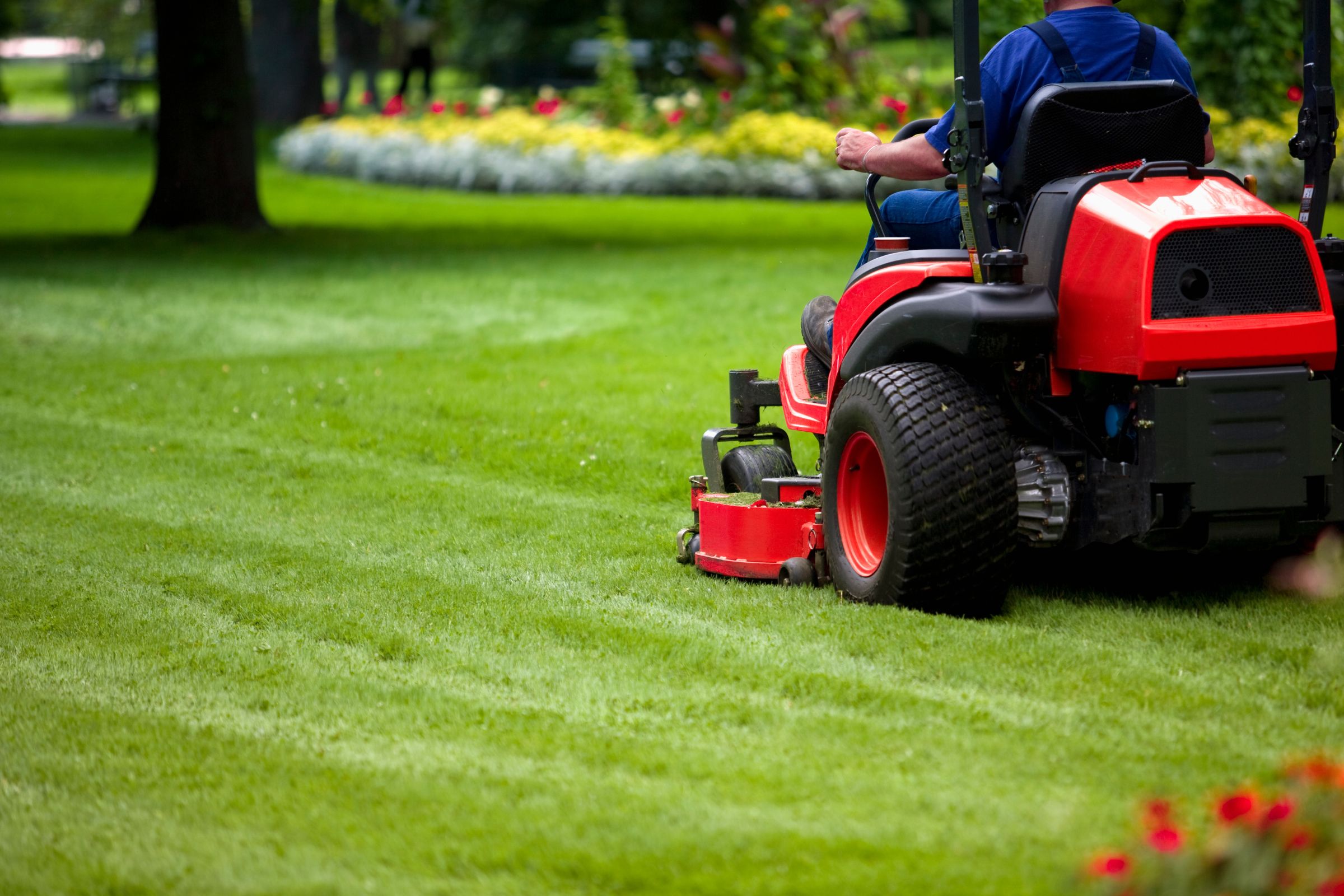
Massachusetts’ independent schools and cultural institutions take pride in their well-kept grounds, but landscaping and lawn maintenance carry risks that require careful management. Operating mowers, handling chemicals, or navigating uneven terrain can lead to injuries if safety measures aren’t in place. The Independent Schools Compensation Corporation (ISCC) supports its members in creating effective safety programs to reduce these risks, protect employees, and maintain thriving campuses.
This article outlines practical steps tailored for schools and cultural institutions. These strategies aim to minimize accidents, cut workers’ compensation costs, and promote a safer workplace.
Why Landscaping Safety Is Essential
Landscaping involves physical tasks and equipment that can cause harm without proper precautions. A single incident can lead to medical expenses, lost productivity, or reputational challenges. For schools and cultural institutions with limited budgets and high community expectations, preventing injuries is a must.
A strong safety program ensures compliance with OSHA regulations while creating an environment where employees feel valued and protected. Here’s how to build one, step by step, with actionable advice for administrators, facilities managers, and groundskeepers.
Step 1: Establish a Safety-First Mindset
Create a Clear Safety Policy Statement
A concise safety policy statement sets the tone for your commitment to employee well-being. Display it prominently in break rooms or on bulletin boards and ensure all staff understand it. For example:
“[Your Institution] is dedicated to a safe workplace. We enforce safe practices in all landscaping tasks to protect our staff, visitors, and property.”
Involve Leadership & Staff
Safety succeeds when everyone participates. Leaders should provide resources—time, training, and equipment—while welcoming staff feedback. Groundskeepers, who face daily hazards, offer valuable insights for practical policies. Regular safety discussions, whether in meetings or quick check-ins, keep the focus consistent.
Step 2: Train For Success
Begin With Thorough Orientation
New hires need immediate safety training before handling equipment. Cover:
- Hazard identification: Recognizing risks like uneven ground or worn tools.
- Emergency protocols: Steps to take during an accident.
- Equipment basics: Safe startup, operation, and shutdown procedures.
Assign them to work alongside an experienced employee for hands-on guidance during their initial months.
Maintain Ongoing Training
Safety requires regular reinforcement. Hold monthly safety meetings (15-20 minutes is often enough) to address topics like seasonal risks (e.g., slippery leaves in fall) or updated equipment guidelines. Document these sessions to track participation and ensure accountability.
Step 3: Implement Safe Practices
Equipment-Specific Protocols
Each tool carries unique risks. The guide provides detailed procedures, including:
- Riding Lawn Mowers:
- Inspect for debris before starting.
- Use seat belts and roll-over protection structures (ROPS).
- Mow slopes cautiously—across for walk-behind mowers, up-and-down for riders.
- Grass Trimmers:
- Wear eye and hearing protection.
- Keep cords behind you to avoid tripping or cutting them.
- Power off before clearing debris.
- Chemical Handling:
- Read labels and wear PPE like gloves and goggles.
- Store chemicals securely, away from heat sources.
Maintain a Clean Workspace
Good housekeeping prevents accidents. Clear clippings, store tools properly, and address spills immediately. These habits reduce trips, slips, and equipment-related mishaps.
Step 4: Respond & Refine
Investigate Incidents Thoroughly
When an accident or near-miss occurs, focus on finding the cause, not assigning blame. Was it a lack of training? A faulty tool? Use the findings to improve your program, such as adding a training session or repairing equipment.
Conduct Regular Inspections
Routine checks of grounds and equipment can catch issues early. Encourage groundskeepers to report wear, hazards, or potential environmental risks—such as overgrown brush that could harbor ticks—during daily tasks. Address problems quickly and document them for future reference.
For additional guidance on outdoor worker protection, see our tick bite prevention tips.
Step 5: Manage Specialized Risks
Chemical Safety
Landscaping often involves pesticides or fertilizers. Train staff on safe mixing, application, and disposal. Keep Safety Data Sheets (SDS) accessible and ensure spill kits are available.
Personal Protective Equipment (PPE)
PPE, from sturdy boots to respirators, is essential. Supply it, train employees on proper use, and replace worn items promptly to maintain protection against unexpected hazards.
Learn More: Essential Safety Tips for Outdoor Work & Maintenance For ISCC Members In Massachusetts
The Benefits: A Safer, More Productive Team
These steps meet regulatory requirements, and can transform your landscaping operations. Fewer injuries translate to lower costs, better employee morale, and a stronger reputation as a responsible employer. For independent schools and cultural institutions, this aligns with values of care and community.
The ISCC is here to help. Access our resources—sample policies, training materials, and expert guidance on our website to start or enhance your safety program.
Take Action Today:
- Draft your safety policy this week.
- Plan a team training session for this month.
- Inspect your equipment before the next job.
By implementing these measures, you’re creating safer grounds and a stronger future for your institution.